Part I
Building Information
Building Name |
Coppin State Science And Technology Center |
Location |
Baltimore, Maryland |
Building Occupant |
Coppin State University |
Occupancy Type |
Business (B) |
Size |
135,000 GSF |
Number of Stories Above Grade |
4 Plus Penthouse |
Building Timeline |
October 2012 – October 2014 |
Overall Project Cost |
$76.2M |
Project Delivery Method |
CM at Risk |
Project Team
Owner │ University of Maryland │ www.umd.edu
Construction Manager │ Barton Malow Company │ www.bartonmalow.com
Architect │ Cannon Design │ www.cannondesign.com
Mechanical & Electrical Engineer │ Cannon Design │ www.cannondesign.com
Civil Engineers │ Site Resources, Inc. │ www.siteresourcesinc.com
Landscape Architect │ P.E.L.A. Design, Inc. │www.peladesign.net
Structural Engineer │ Columbia Engineering, Inc. │ www.columbiaengineering.com
Geotechnical Engineer │ T.L.B. Associates, Inc. │ www.tlbinc.net
Plumbing / Fire Protection Engineering│ WFT Engineering, Inc. │ www.wfteng.com
Architecture
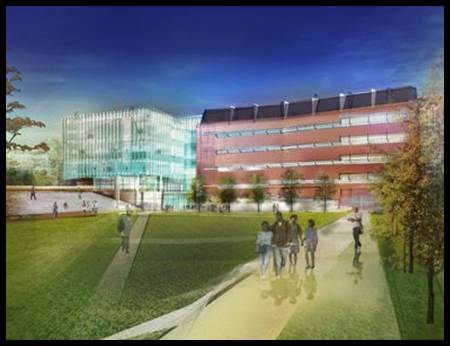
Figure A - Rendering from Northeast Corner |
|
Figure B - Rendering from Southwest Corner |
Images Courtesy of www.coppin.edu/CapitalPlanning/STC.aspx
The New Science and Technology Center (STC) is located on southern end of Coppin State University’s Campus in the northwest suburbs of Baltimore, Maryland. The Project requires the demolition of approximately 210 residences on the south side of campus. After rough grading and the installation of a rammed aggregate pier system, the new 4-story concrete building will be constructed providing for the critical needs in science related disciplines on campus. It will include classrooms and areas for the Departments of Mathematics and Computer Science and Natural Sciences as well as the Information Technology Division.
In comparison to the rest of the CSU campus, the architectural design of the STC includes sleek lines and a modern façade. The surrounding area buildings have typical brick facades with rectilinear building footprints. With this new design, the glass curtain walls add a modern and lively touch to the campus while still tying into the existing brick architecture. The new building is situated to the east of the new state-of-the-art Health and Human Services Building, which has very similar architecture. These buildings as well many others are part of Coppin State’s mission of expanding and creating a more attractive campus environment.
Code
The proposed type of construction for this single building is classified as Type 1B under IBC 2009. The building’s occupancy includes three classifications: high-rise buildings, atriums, and hazardous materials. The accessory occupancy (lecture hall) is assembly A-3 and no separation is required due to the minimal building area. The height limit is set at 11 stories or 160’ per IBC 2009 and is granted an additional 1 story/20’ for fully sprinklered building.
The following national code models were utilized in this design:
- IBC 2009
- NFPA 2009
- IMC 2009
- IPC 2009
- NSPC 2006
Zoning
Due to the approximate 210 houses on the proposed building footprint for the new Science and Technology Center, Coppin State University requested the release of part of the deed of trust that was held on the single family units. The existing area was zoned at R-7 and R-8, both residential areas. With the successful release of the lien, Coppin State University now has the authority to build a class B building on the newly zoned land.
Historical Requirements
There are no historical requirements for this building.
Building Enclosure
Major components of the building enclosure include a large glass curtain wall façade on the north end while a brick façade accents the main building structure. The square offset glass curtain wall on the north end attracts the viewer’s eye to the building and opens to the grassy quad on the east side. The sections below show greater detail of the building’s enclosure and the materials that are being used.
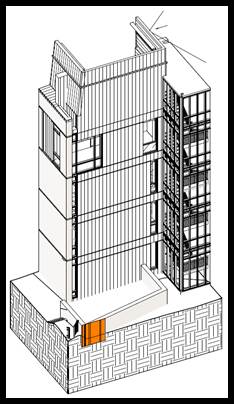 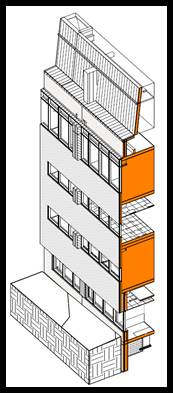 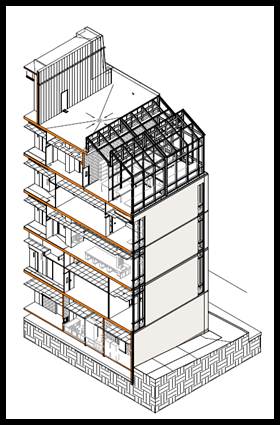 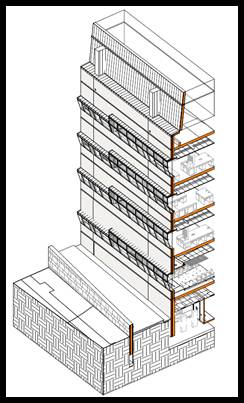
Figure 1 - North |
|
Figure 2 - East |
|
Figure 3 - South |
|
Figure 4 - West |
Detail 5 - A0416 |
|
Detail 6 - A0417 |
|
Detail 5 - A0410 |
|
Detail 4 - A0411 |
North
The north façade of the building includes the large cubicle glass curtain wall. The majority of the glass panels are constructed of 1” insulated (Low-E) Glazing that are either heat strengthened, laminated, tempered, or contain a patterned frit.
East
Looking in more detail at the east façade, there is a mix of small curtain walls set into a brick veneer. The glazing is of the same material listed for the north façade. Extruded Tuscan Series Red Cliff brick make up main brick while a Manganese Ironspot Smooth color brick is used for the accents on the façade.
South
The southern elevation is has a majority of curtain walls on the western side where it fades into a larger use of brick veneer and concrete on the eastern side. There is an exposed concrete wall at level 1 and below on the east face of the south elevation.
West
With the exception of more curtain wall area, the west building enclosure reflects very closely to that of the east. A mix of smaller curtain wall glazing is found throughout the majority of the west elevation. The other side of the atrium-like glass curtain wall can be seen on the north end.
Sustainability
The Science and Technology Center is required to reach a minimum of LEED Silver Certification, but is tracking to achieve LEED Gold Certification with the current design. Some LEED categories include the site location, water efficiency, energy consumption, recycled material, and indoor air quality. The site is in an urban area where public transportation can be utilized and the open quad area preserves pervious surfaces. The low-E glass mentioned earlier will help reduce energy consumption as well as the variable speed drives of the mechanical systems. In addition, the project has a goal of recycling up to 75% of construction waste. Furthermore, particular sustainable devices integrated into the building design include a rainwater collection system, a green roof, sun shades, high efficiency boilers and chillers, and a complex insulation backing system behind the metal panels to minimize thermal bridging.
Part II
Construction
The Science and Technology Center is under a strict construction timetable due to initial project delays that pushed construction back almost 3 months. Approximately 210 row homes stood in place where the new building would stand. It was through property acquisition issues that caused the initial large delay. More than half of these properties were found to have asbestos-containing material and abatement and clearing procedures were planned. This delay put pressure on the project team to find areas in the schedule for acceleration and using different means and methods. As the original schedule outlines, the building will be constructed with two phases—North and South—and progress upwards through the four floors and penthouse. With the building in the early stages on construction, opportunities for schedule acceleration will be of high importance—the exterior envelope construction methods will provide chances to gain back schedule time.
A foreseen constructability challenge includes the intense waterproofing details in many areas. These include the thresholds where materials change types and also at the top of the curtain wall near the parapet. The waterproofing membrane and air barrier require integration between installation of two different systems, and consequently two different subcontractors. These areas should be of high focus to eliminate any future maintenance issues with the building envelope.
In addition to the waterproofing detail, the curtain wall and masonry wall construction deem another constructability issue in terms of schedule duration. A stick-built system of 2” HSS connections, aluminum frames, and 1” glazing will be one of two items on the schedule that endure the most installation time—the second being the masonry wall construction. As the project progresses, these areas can be the focus of major cost and time savings with alternative installation methods.
Electrical
The main building switchboard is rated for 4000A, 480/277V at 3 Phase. It is with this that 6 transformers supply power to the building. The lower level main transformer is a general duty dry type transformer with an integral USS rated at 2500kVA. From this branch, four other transformers supply each of the floors 1-4. The remaining transformer is located at the lower level. The main building load was designed for 3,066,675 VA and 3690 amps. In addition, the emergency power system is supplied by two generators (750kW and 500kW).
Lighting
The lighting plan for the STC Building involves a combination of compact fluorescent down lights, different sizes of T5 fluorescent troffer luminaires, and wall mount pendant fixtures. The main lobby utilizes a majority of suspended direct linear fluorescent F28T5 luminaires with a single lamp. When looking at the typical classroom and lecture hall, a linear direct/indirect pendant type luminaire with F28T5 lamps. For a majority of the lab spaces, a 2’x4’ high efficiency recessed troffer luminaire is utilized with 3-F28T5 lamps. The general spaces on the lower level and storage areas impose 4’ surface-mounted strip industrial reflector luminaires. The typical lamp type throughout the entire building is a F28T5.
Mechanical
This building is supported by 6 different VAV Trane air handling units (AHUs), 4 cooling towers and multiple boilers, lab exhaust fans, and computer room air condition units. This is due to the mixed-use of this facility and has many requirements to fulfill. There are three large AHUs with total CFM ranges from 23,500-44,500 that serve the building’s main floors. The remaining 3 AHUs with total CFM ranges from 3,200-4,500 serve the lower levels and the lecture hall area. Being that a large portion of this building is represented by laboratories, there are a major number of exhaust fans to serve each of these areas. Also, fin tube radiators supply supplemental warm air along the window line of each space to aid the central AHU. Much of these systems also include areas for schedule acceleration due to the system type and installation labor necessary.
Structural
The structure of this building is supported by foundation walls (12” to 24” thick) and spread footings (5’x5’ up to 14’x14’) bearing on suitable soil on the north end and geopiers on the south. The geopiers on the south end support loads ranging from 80 kips to 980 kips, depending upon location on the building footprint. The cast-in-place structure for the floors 1-4 incorporate elevated concrete slabs supported by concrete beams and columns. The concrete columns range from 20”x20” to 28”x28” square columns and 32” diameter circular columns. The concrete beams supporting the slabs have various sizes ranging from 16”x24” to 30”x48”. Elevated concrete slabs are to be 12” thick normal weight concrete reinforced with #4 rebars at 9” on center as top and bottom mat bars. A thickness of 8” (20” total slab thickness) at locations of drop panels around the columns is required.
Structural steel is then used for the design of the penthouse above the fourth floor. Composite metal decking will top off the structural frames and provide the support for the roof system. Typical beam sizes include W14x22 and W16x26. A typical roof frame utilizes W14x61 columns (20’ in height) and W18x35 beams (~25’ in length). The stairwells and partials floor space also include structural steel members. In total, the steel bid package was estimated at $750,000.
Fire Protection
The entire building, including all mechanical and electrical rooms is protected with a fully automatic combination standpipe-sprinkler system (Class 1). In addition all unconditioned spaces subject to temperatures less than 40°F will be protected by a dry-type sprinkler system. Sprinklers will also be supplied at the top and bottom of elevator shafts. The campus datacenter, the main distribution frame telecommunication and electrical room #3 will be protected with a fully automatic, total flooding clean agent fire suppression system. The room enclosures will also be protected with a single-interlock preaction sprinkler system.
Security & Technology
The Science and Technology Center will integrate new door/gate access controls (card) and intrusion detection through video surveillance (CCTV). This will include the installation of the following items: fiber optic cabling and patch panels, network video recorders, uninterruptible power supply, and a single monitor computer for control of the system. In addition to these security items, many of the rooms will be supplied with projectors, screens, and multiple computer stations. This will provide the newest technology for students on campus and will serve as the main computer labs. |